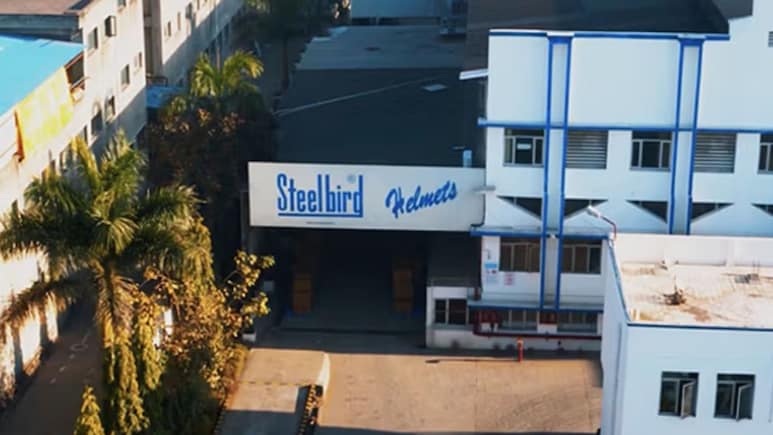
Steelbird Hi-Tech India Limited, the Indian helmet manufacturer, is accelerating its production capabilities and expanding its technological edge to manufacture
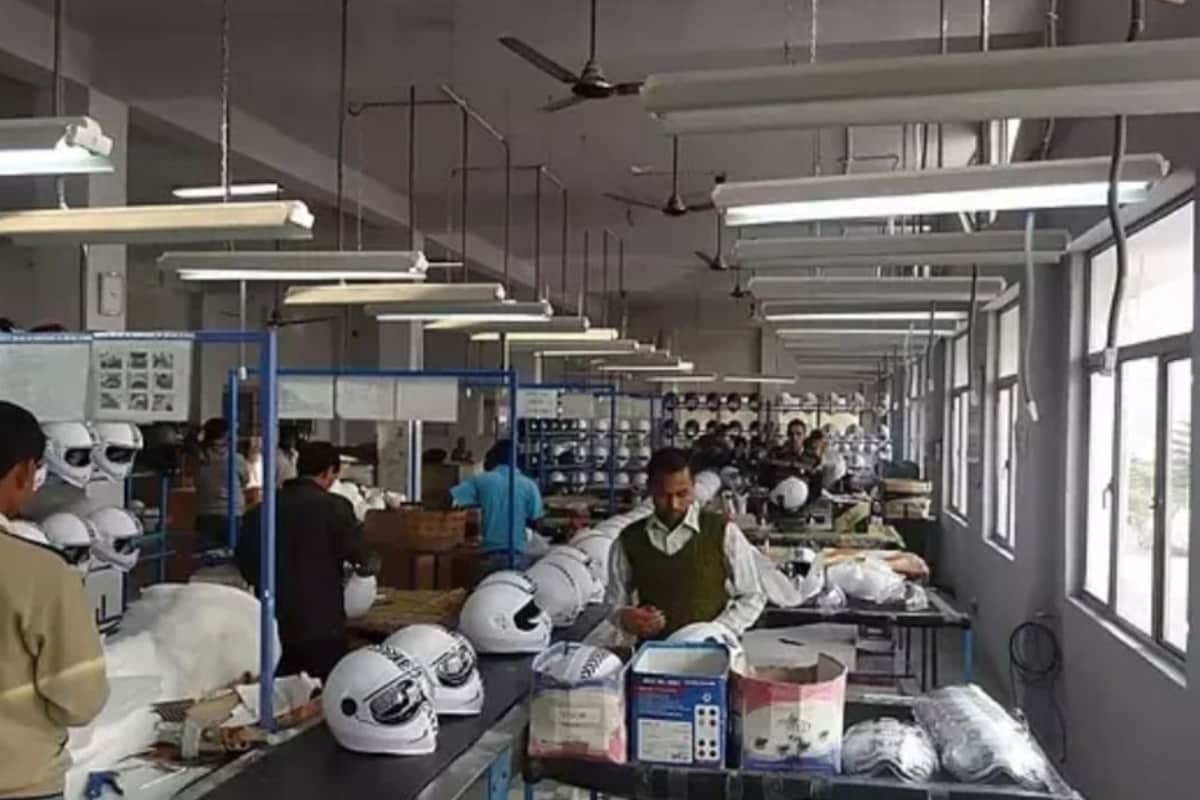
over 60,000 helmets per day. With enhanced in-house operations and the development of cutting-edge infrastructure, the company is preparing for a landmark year in its growth journey.
In the last financial year, Steelbird completed a capital expenditure (capex) of Rs 54 crore, and in the current financial year, the company is undertaking an additional Rs 50 crore capex to expand existing plant and machinery. This will take total installed capacity beyond 60,000 helmets per day, reflecting Steelbird's commitment to scale while maintaining complete control over quality.
The company's EPS plant, covering 7,500 square meters, currently produces 45,000 EPS units daily, with the added capacity to manufacture EPP products. Its Decal plant delivers 14,000 decals per day. The Company has already invested Rs 40 crore, dedicated to infrastructure for EPS, EPP, and decals alone.
Steelbird is actively planning the establishment of a dedicated carbon fiber helmet manufacturing plant, aimed at producing all-carbon fiber helmets entirely in-house. As part of this initiative, the company is also planning to set up India's first in-house carbon fiber and fiberglass weaving facility. This integrated setup is being designed to reduce dependency on external material suppliers and enable complete control over material quality and performance. Through this facility, Steelbird is planning to explore and develop diverse hybrid material combinations and innovative weave structures, aiming to enhance the strength, reduce the weight, and improve the impact resistance of helmet shells.
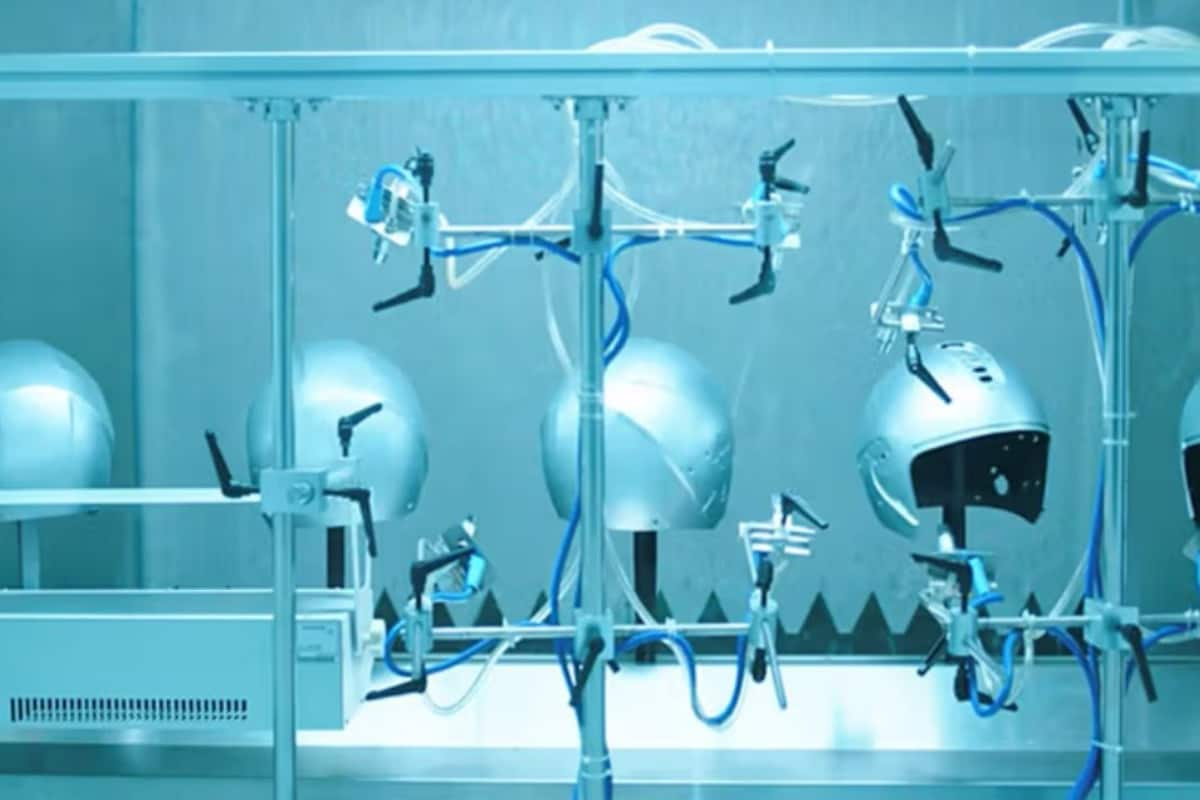
Mr. Rajeev Kapur, Managing Director, Steelbird Hi-Tech India Ltd., said, "Every helmet component at Steelbird is made in-house to maintain the highest safety standards. We do not rely on third-party workers, because even a small deviation in production parameters can compromise safety. Quality is non-negotiable for us."
Also Read: Maruti Suzuki XL6 Launched With Six Airbags As Standard; Check Prices
Steelbird is actively investing in innovation and product development to strengthen its position in the rapidly growing helmet market. Recognizing the increasing consumer demand for enhanced safety, smart features, upgraded technologies, and fashion-oriented designs, the company has outlined an ambitious product roadmap. In the current financial year, Steelbird plans to introduce 15 new helmet models to the market. Building on this momentum, the company aims to launch 10 new models every subsequent year to consistently refresh its portfolio and meet evolving customer expectations. This proactive strategy is driven by the market's shift towards helmets not just as safety gear, but as technology products, lifestyle accessories, and designer statements.
Developing a new helmet model involves a significant investment, typically ranging from Rs 1.5 crore to Rs 10 crore, and requires a development cycle of 2 to 3 years, depending on the complexity, design, and technological integrations involved.
Track Latest News Live on NDTV.com and get news updates from India and around the world